The Advantages of Using Tungsten Carbide Material for various Applications
By:Admin
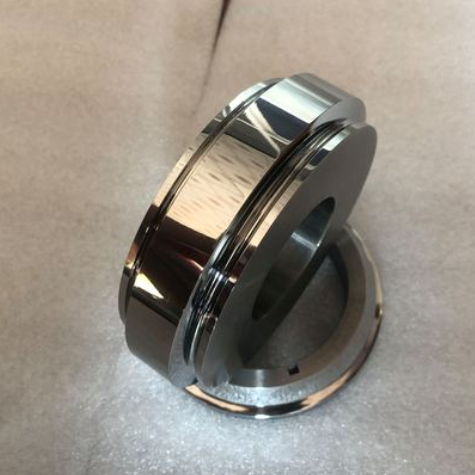
Introduction:
In today's ever-evolving industrial landscape, material innovation plays a crucial role in driving progress and shaping the future. Among the various groundbreaking materials being developed, Tungsten Carbide stands out as a true champion. Renowned for its unrivaled durability, versatility, and exceptional performance, Tungsten Carbide offers a multitude of opportunities across a wide range of industries. This revolutionary material is changing the way we approach manufacturing, engineering, and beyond.
Unleashing the Potential: Tungsten Carbide Material
Tungsten Carbide has emerged as a game-changer in the world of material science. Prominent for its superior hardness, tensile strength, and resistance to wear and corrosion, this metallic compound has proved to be a standout performer in numerous sectors.
1. Manufacturing Reinvented:
The manufacturing industry, known for its relentless pursuit of efficiency and excellence, has found a perfect partner in Tungsten Carbide. With a hardness comparable to that of diamond, this material has become a go-to choice for tools and machinery applications. It significantly enhances the lifespan of cutting tools, drills, dies, and molds, making them last longer while withstanding extreme conditions. Manufacturers can now achieve increased productivity, reduced downtime, and improved output quality, resulting in unparalleled cost-effectiveness.
2. Revolutionizing Engineering:
Tungsten Carbide has revolutionized the engineering landscape by providing engineers with an array of possibilities. From aerospace to automotive applications, its high melting point, low thermal expansion, and exceptional strength are invaluable in the development of high-performance components. The material's remarkable wear resistance allows engineers to create longer-lasting turbine blades, bearings, gears, and various other critical parts. As a result, industries can now produce efficient, safe, and durable equipment, contributing to the advancement of technology and human progress.
3. Mining and Extraction Advancements:
With the mining and oil industry pushing the boundaries of extraction techniques continually, Tungsten Carbide proves to be an indispensable asset in the quest for better efficiency and productivity. The material's excellent abrasion and erosion resistance make it ideal for drilling bits, compacted tooling, and other underground applications. By implementing Tungsten Carbide into their mining operations, companies can experience enhanced penetration rates, reduced maintenance costs, and improved overall performance, leading to increased profitability and sustainability.
4. Beyond Industrial Applications:
Tungsten Carbide's versatility extends beyond heavy machinery and industrial components; its ability to withstand extreme conditions and retain superior toughness opens doors for diverse applications. For instance, in the jewelry industry, Tungsten Carbide has gained popularity for its scratch resistance, lustrous appearance, and long-lasting beauty. Similarly, the medical field utilizes this remarkable material in surgical tools, implants, and prosthetic devices, thanks to its biocompatibility and wear resistance. The possibilities seem infinite, as Tungsten Carbide continues to innovate various other niche sectors.
Conclusion:
As Tungsten Carbide material continues to make waves across industries, its unparalleled durability, versatility, and exceptional performance capture the attention of manufacturers, engineers, and beyond. From manufacturing to mining, this revolutionary material empowers industries to embrace unparalleled cost-effectiveness, efficiency, and productivity. Its remarkable properties enable the creation of tools and components that withstand the harshest environments while maintaining peak performance. As innovation propels us forward, Tungsten Carbide remains at the forefront, reshaping industries and setting new standards for excellence.
Company News & Blog
Discover the Key Benefits of Tungsten Carbide Bushing Die According to the Latest News
Tungsten Carbide Bushing Die (need remove brand name) Is The Leading Choice For Precision ManufacturingWith over 20 years of experience in the tungsten carbide industry, (brand name) has become the leading provider of precision machining solutions for customers in various industries. The company specializes in producing high-performance tungsten carbide bushing dies that can help improve production efficiency and reduce costs.Tungsten carbide is a powerful and durable material that can withstand high temperatures and pressure. It is ideal for use in precision machining because of its hardness and strength, making it the perfect choice for dies in the manufacturing process. When combined with steel, tungsten carbide provides a unique blending that combines toughness and wear resistance with the ability to retain sharp cutting edges.The tungsten carbide bushing dies offered by (brand name) are designed to deliver consistent performance even in the most challenging environments. These bushing dies are commonly used in the production of wire and cable, rubber and plastics, and metalworking industries. With their high resistance to wear and superior accuracy, these dies ensure that products meet the exacting standards of customers and end-users.(brand name) specializes in producing bushing dies that can be customized to meet specific customer requirements. The company has a team of experienced engineers who use advanced CAD/CAM software to create high-precision tooling that is tailored to individual customer needs. The company's dies are used by customers around the world, including China, the United States, and Europe.The tungsten carbide bushing dies produced by (brand name) have several advantages over traditional steel or ceramic dies. Tungsten carbide is much more durable than steel, making it less prone to wear and tear. It is also more resistant to corrosion and can withstand extreme temperatures and pressures. This means that tungsten carbide dies last longer and require less maintenance than other materials.Another advantage of tungsten carbide is its high coefficient of friction. This means that less lubrication is required during the manufacturing process, reducing overall costs. Additionally, tungsten carbide dies require less power to operate than other materials, reducing energy costs and improving efficiency.The quality of tungsten carbide bushing dies can significantly impact an organization's productivity and profitability. With over two decades of experience in the industry, (brand name) has become the leading provider of high-quality, precision tungsten carbide machining solutions. The company's dedication to providing customized products and exceptional customer service has made it a trusted partner to organizations around the world.In conclusion, the tungsten carbide bushing dies produced by (brand name) are an essential component of precision machining processes used by leading manufacturers globally. The company's commitment to quality and service has made it the first choice for customers in various industries. With its team of experienced engineers and advanced production capabilities, (brand name) is well-positioned to continue leading the industry in the production of high-performance tungsten carbide bushing dies.
Tungsten Carbide Bushing Grade: A Comprehensive Guide to its Properties and Applications
article:Tungsten Carbide Bushing Grade: The Ultimate Solution to Wear ResistanceWhen it comes to mechanical applications, wear resistance is a primary concern. Over time, even the strongest materials wear down, creating a need for regular maintenance or replacement. However, with the advent of tungsten carbide bushing grade, the game has changed, and wear resistance is no longer a concern.Tungsten carbide is a versatile material that combines the hardness and strength of metallic tungsten with the toughness and ductility of a carbide. With its excellent wear resistance and toughness, it is highly desirable for a range of industrial applications.One of the key applications of tungsten carbide is the production of bushings, which are critical in manufacturing and construction. Bushings play a vital role in reducing the friction and wear between machine parts, ensuring the smooth and efficient operation of machinery.The use of tungsten carbide bushing grade has revolutionized the way industrial machinery works, creating a more efficient and effective system. The tungsten carbide bushings have a high wear resistance, which leads to longer service life and reduced maintenance costs. In addition, the material has a low coefficient of friction, reducing the amount of energy needed to operate the machinery and resulting in lower operating costs.The combination of the high wear resistance and low coefficient of friction makes tungsten carbide bushing grade the ideal material for a range of industrial applications, including mining, construction, oil and gas, and manufacturing.One company that has been at the forefront of the production of tungsten carbide bushing grade is {company name}. With its state-of-the-art manufacturing facilities, the company produces high-quality tungsten carbide bushings that meet industry standards and exceed customer expectations.Founded in {year}, {company name} is a global leader in the production of tungsten carbide products, offering a wide range of products and services to customers worldwide. The company has a team of highly skilled and experienced professionals who are committed to delivering excellence in every project.In addition to its production line, {company name} provides its customers with technical support and solutions to their specific needs. The company's engineers work closely with customers to understand their needs and requirements, providing customized solutions that address their unique challenges.{Company name} has a robust quality control system that ensures all products meet the highest standards. The company uses advanced technology and equipment to test the quality and performance of its products, ensuring that only the best products are delivered to customers.The company's commitment to excellence has earned it a reputation as a leader in the industry, with customers from around the world relying on its products and services to keep their machinery running smoothly.In conclusion, tungsten carbide bushing grade is a game-changer when it comes to wear resistance in industrial applications. With its high wear resistance and low coefficient of friction, it is the ideal material for a range of industries, from mining to manufacturing.Companies like {company name} are at the forefront of the production of tungsten carbide bushings, providing high-quality products and solutions to customers worldwide. With their commitment to excellence and customer satisfaction, companies like {company name} are helping to shape the future of industrial machinery and production.
Carbide Nails: Revolutionary Die Technology Shaping the Future of Nail Production
Innovative Carbide Nail Making Die Revolutionizes Nail Manufacturing[Company Name], a leading manufacturer of cutting-edge industrial tools and equipment, has recently launched a revolutionary carbide nail making die. This advanced technology is set to transform the nail manufacturing industry, providing a superior solution that enhances efficiency, durability, and overall productivity.The carbide nail making die, developed by [Company Name]'s team of experienced engineers and knowledgeable researchers, is a ground-breaking innovation in the field. This cutting-edge product is designed to deliver unparalleled precision and quality in the production of nails, catering to the diverse needs of various industries worldwide.Traditionally, nail manufacturing has predominantly relied on conventional dies made of steel. However, these conventional steel dies have numerous limitations, including a limited lifespan and the need for frequent repairs and replacements. [Company Name]'s carbide nail making die aims to overcome these challenges by utilizing the exceptional properties of carbide materials.Carbide, a compound of carbon and metal, possesses remarkable toughness, hardness, and heat resistance. By harnessing the inherent benefits of carbide, [Company Name] has successfully developed an innovative die that offers extended life expectancy, reducing downtime and enhancing overall productivity. The durability of the carbide nail making die ensures consistent nail quality throughout the production process, minimizing the need for adjustments and repairs.Furthermore, the carbide nail making die provides enhanced precision and accuracy, resulting in nails with consistent dimensions, smooth finishes, and reduced defects. This improvement in quality not only satisfies the stringent requirements of industries such as construction, carpentry, and furniture manufacturing but also meets the growing demands of discerning consumers who seek high-quality products.Another key advantage of [Company Name]'s carbide nail making die is its exceptional resistance to wear and tear. The innovative design and fabrication process ensure that the die remains sharp and maintains its cutting edge for extended periods even when subjected to continuous stress. This significantly reduces downtime and increases production capacity, allowing manufacturers to meet tight deadlines more effectively.The introduction of the carbide nail making die by [Company Name] aligns seamlessly with their commitment to technological advancements and innovative solutions. Driven by a philosophy of providing the best tools for industrial processes, they continually invest in research and development to meet the evolving needs of their customers.As [Company Name] introduces this revolutionary product to the nail manufacturing industry, they aim to enhance competitiveness and productivity. By minimizing production costs and maximizing output efficiency, manufacturers can optimize their operations and ultimately deliver greater value to their clientele.The potential impact of [Company Name]'s carbide nail making die extends beyond the realms of industrial production. As the construction and manufacturing industries increasingly emphasize environmental sustainability, this innovative technology contributes to reducing waste by ensuring fewer defective nails and minimizing the usage of materials, ultimately reducing the environmental footprint.In conclusion, [Company Name]'s introduction of the carbide nail making die sets a new standard in the nail manufacturing industry. By harnessing the exceptional properties of carbide materials, this advanced technology enhances durability, precision, and overall productivity. As this ground-breaking innovation gains traction, manufacturers across various industries can look forward to optimizing their operations and meeting the demands of the modern market.
Discover the Power of Cemented Carbide in the YG8 Variety
Cemented carbide is a widely used material in various industries because of its excellent physical and mechanical properties. Of the many cemented carbides available, YG8 cemented carbide (brand name needs to be removed) is a popular choice because of its outstanding hardness, toughness, and wear resistance. This cemented carbide is made from a mixture of tungsten carbide (WC) and cobalt (Co) in precise proportions, resulting in a material that is not only durable but also highly resistant to impact and corrosion.One company that specializes in the production of YG8 cemented carbide products is committed to delivering reliable and high-quality carbide products to its customers. As a leading manufacturer in the cemented carbide industry, our company has been dedicated to the research and development of new products, ensuring that our customers have access to more specialized and customized carbide solutions.Our YG8 cemented carbide products are available in a variety of shapes, including rods, plates, blades, and other complex geometries. These products have been used in numerous applications, such as cutting tools, drill bits, saw blades, wear parts, and more. Because YG8 cemented carbide is an excellent conductor of heat, it is also commonly used in the manufacturing of thermal conductor alloys.The company’s advanced production process includes strict quality control procedures and cutting-edge technology to ensure that every product leaving our facility meets and exceeds the industry's high standards. Our production equipment is regularly updated to incorporate the latest technology trends, which helps us remain a leader in the industry.The durability and strength of YG8 cemented carbide make it a reliable material for use in challenging environments. Its corrosion-resistant properties make it an ideal material for use in harsh chemical and extreme temperature environments. Our cemented carbide products are maintained at the most stringent of manufacturing standards, ensuring that they perform exceptionally well in the most challenging of working environments.At our company, we consistently strive to ensure that our customers' expectations are exceeded. We take pride in our state-of-the-art research and development capabilities, which allow us to tailor our cemented carbide products to meet our customers' specific requirements. Our customer base ranges from small to large corporations with varying requirements, and we work closely with each customer to ensure that their every need is met.Our team of highly skilled professionals is poised to help our customers navigate through the ordering process. Our team is knowledgeable about different cemented carbide products that are available in the market and is always eager to help customers identify the most suitable product for their needs. We work collaboratively with our clients, first to understand their specific needs and then, to provide a customized solution that satisfactorily meets their needs. We also offer after-sales services, which ensures that customers receive prompt and necessary support when required.In conclusion, YG8 cemented carbide (brand name needs to be removed) is an incredibly durable and robust material that has various applications. As a leading manufacturer of cemented carbide products, our company is continuously committed to delivering high-quality products that meet our customers' requirements. Our advanced production process, coupled with our state-of-the-art equipment technology, sets us apart from our competitors in the industry. We pride ourselves on being transparent with our customers, and we collaborate with them to ensure that their cemented carbide solutions are of the highest quality and meet and exceed their expectations. With our customer-centric approach, we are confident in our ability to continue providing unparalleled support to our customers.
Cemented Carbide Rods: Durable Tools for Various Industries
Cemented Carbide Rods - Providing High-Quality Performance and DurabilityCemented Carbide Rods are an essential tool in the manufacturing industry. These high-performance components are made from a combination of tungsten carbide and cobalt, which makes them incredibly durable and resistant to wear. They are used to cut, shape, or drill different materials to produce a wide range of products.One company that has been at the forefront of producing high-quality cemented carbide rods is {name of company}. The company has been in operation for many years and has gained a reputation as a leader in the manufacturing of carbide tools. The company's success can be attributed to its state-of-the-art manufacturing processes, excellent customer service, and commitment to producing high-quality products.Cemented carbide rods are used in a variety of industries, including mining, construction, automotive, and aerospace. These industries demand high-performance and durable tools that can withstand the harsh environments they work in. Carbide rods are an ideal choice because they are made from a combination of tungsten carbide and cobalt, which makes them highly resistant to wear and corrosion.The manufacturing process of cemented carbide rods involves several stages, including powder preparation, pressing, presintering, sintering, and finishing. {name of company} uses advanced technology and state-of-the-art machinery to ensure that every step of the process is done correctly, resulting in high-quality products. The company's production line can produce a range of rod sizes and lengths to meet customer requirements.One unique feature of {name of company}'s cemented carbide rods is that they are available in different grades. The company offers standard grades, which are ideal for general machining applications, and special grades that are designed for specific applications. The special grades are tailored to meet the demands of specific industries, resulting in higher efficiency and productivity.In addition to producing high-quality cemented carbide rods, {name of company} also offers other carbide tools, including end mills, drill bits, and inserts. The company's product range is extensive, ensuring that customers can find the right tool for their application. The company also offers customized solutions for customers who have specific requirements or special applications.Customer service is a top priority for {name of company}, and the company has a team of experts who provide technical support and advice to customers. The team can help customers choose the right tool for their application and provide recommendations on how to optimize their machining processes. The company's commitment to customer service has helped it gain a loyal customer base, with many customers returning to purchase more products.In conclusion, cemented carbide rods are an essential tool in the manufacturing industry, and {name of company} has established itself as a leader in the production of high-quality carbide tools. The company's commitment to producing high-quality products, using advanced technology and state-of-the-art machinery, has resulted in products that are highly durable, resistant to wear, and ideal for demanding applications. The company's extensive product range, coupled with its commitment to customer service, has made it a preferred choice among many customers.
The Versatility and Durability of High-Quality Tungsten Carbide Cutter Blades Revealed in Latest News
Tungsten Carbide Cutter Blade: The Heavy-Duty Precision Tool for Industry ApplicationsTungsten Carbide Cutter Blade, the precision tool that has been transforming the industry with its heavy-duty cutting capabilities, is a name that has become synonymous with excellent craftsmanship and reliability. Used in a wide range of industrial applications, Tungsten Carbide Cutter Blade has earned a reputation for being the go-to precision tool for the toughest jobs in construction, manufacturing, and even the metalworking industry.What Makes Tungsten Carbide Cutter Blade Unique?Tungsten Carbide Cutter Blade offers a unique combination of toughness, strength, and durability, which is why it is unmatched in the industry. It is specifically designed to outlast other blades and withstand heavy-duty cutting tasks that would otherwise require multiple blades, which saves time and improves productivity.One of the unique features of the Tungsten Carbide Cutter Blade is its use of tungsten carbide, one of the toughest and densest materials on the planet. When combined with other metals such as cobalt, tungsten carbide forms a compound known as cemenite, which is a very hard and durable material that can withstand high levels of stress. The result is a blade that can cut through almost any material with ease, including wood, metal, and even concrete.Another key feature that sets Tungsten Carbide Cutter Blade apart from other blades on the market is its exceptional edge retention. The blade can maintain a sharp edge for longer periods, which reduces the need for frequent sharpening and replacement, making it more cost-effective in the long run.Applications of Tungsten Carbide Cutter BladeTungsten Carbide Cutter Blade can be used in a wide range of applications, including:1. Construction – Tungsten Carbide Cutter Blade can cut through almost any material used in construction, such as asphalt, concrete, bricks, and stones, making it an essential tool for builders, contractors, and masons.2. Metalworking – Cutting metals such as steel and aluminum requires a blade that can withstand high temperatures and stress. Tungsten Carbide Cutter Blade can handle these conditions, making it a top choice for this industry.3. Manufacturing – Tungsten Carbide Cutter Blade is also used in manufacturing, as it can easily cut through materials like plastics, composites, and fibers, while maintaining its sharp edge for longer periods.Company Introduction and InnovationInnovation is at the heart of Tungsten Carbide Cutter Blade's success. The company has been a leader in the industry for over two decades, producing high-quality precision tools that are designed to make cutting tasks easier and more efficient.Tungsten Carbide Cutter Blade's dedication to innovation is evident in the numerous patents it holds for its cutting-edge products, such as its effective design, advanced manufacturing techniques, and rigorous quality control measures.In addition to cutting-edge research and development, Tungsten Carbide Cutter Blade also invests heavily in its manufacturing processes. The company employs state-of-the-art equipment and processes to ensure the highest quality and precision for each blade. From the initial design stage to the final product, Tungsten Carbide Cutter Blade leaves no stone unturned in its drive for perfection.ConclusionTungsten Carbide Cutter Blade is a precision tool that is unmatched in its toughness, strength, and durability. It is the go-to tool for heavy-duty cutting tasks in a wide range of industrial applications, including construction, metalworking, and manufacturing. Its exceptional edge retention and cutting capabilities make it a cost-effective investment that saves time and improves overall productivity. With Tungsten Carbide Cutter Blade, you can be sure of getting the best in heavy-duty cutting tools, made with an unwavering commitment to quality.
Tungsten Carbide Block: A Valuable Industrial Material for Various Applications
Tungsten Carbide Block Emerges as a Game-Changer in the Manufacturing IndustryTungsten carbide is a compound that combines tungsten and carbon, making it a highly versatile material for manufacturing a variety of products. The tough and durable nature of tungsten carbide makes it one of the most preferred materials for applications that require long durability, such as machine parts.Recent technological advancements in the manufacturing industry have given birth to a new product - the tungsten carbide block. These blocks, made from high-quality tungsten carbide, have become a game-changer in the manufacturing industry, as they offer unique properties that traditional materials cannot match.Tungsten carbide blocks are used in various industries, including construction, mining, and manufacturing. They have a wide range of applications that require high wear and abrasion resistance, such as manufacturing cutting tools, dies, and punches. These blocks offer superior performance and longevity compared to other carbide-based materials, making them the leading choice for toolmakers and manufacturers alike.One of the main advantages of tungsten carbide blocks is their ability to withstand high temperatures. The material has a high melting point, making it an ideal choice for applications that require high resistance to heat. Tungsten carbide blocks are also highly resistant to deformation, making them suitable for use in high-pressure environments.Additionally, tungsten carbide blocks exhibit exceptional hardness, providing high wear resistance, and low friction. This unique combination of properties makes the carbide block ideal for applications that require high-precision machining. Many industries, such as the oil and gas and mining sectors, have adopted tungsten carbide blocks due to their outstanding performance in harsh environments.Leading tungsten carbide block manufacturers pride themselves in producing exceptional quality blocks. They focus on using only the best raw materials and state-of-the-art technology to ensure that their blocks meet the most stringent quality standards. This quality-oriented approach has enabled manufacturers to remain the go-to source for manufacturers seeking high-quality tungsten carbide blocks.Tungsten carbide blocks come in different shapes and sizes, catering to various manufacturing applications. Manufacturers can order customized blocks tailored to their specific needs, with varying grades of tungsten carbide to suit the specific application. Additionally, manufacturers can request blocks with different surface finishes to enhance their resistance to wear and corrosion.The growing demand for tungsten carbide blocks has prompted many companies to invest in advanced technology to streamline their production processes. These investments have enabled manufacturers to produce tungsten carbide blocks faster without compromising on quality. Automation has also helped manufacturers to reduce production costs while improving their output.The adoption of tungsten carbide blocks has revolutionized the manufacturing industry, providing manufacturers with cutting-edge technology that improves production performance, longevity, and accuracy. Manufacturers in various industries now have access to a broad range of options to choose from, ensuring that they get the precise block they need for their specific applications.Moreover, by using tungsten carbide blocks, manufacturers can enhance their bottom lines by reducing their production costs and improving the quality of their products. Tungsten carbide blocks are a superior material that is cost-effective in the long run, making them an ideal choice for manufacturers who seek to maximize their profits.The future of tungsten carbide blocks looks bright, with increased investments in R&D that continue to enhance their quality, performance, and durability. Manufacturers can expect to see more advanced products that push the limits of what tungsten carbide blocks can offer.In conclusion, tungsten carbide blocks are a highly durable and versatile material that has revolutionized the manufacturing industry. With their exceptional strength, heat resistance, and wear resistance, these blocks continue to be a game-changer in many industries, providing manufacturers with a cost-effective solution that enhances their performance and bottom line. As the industry continues to invest in advanced technology, manufacturers can expect to benefit from even more innovative tungsten carbide blocks.
High-Performance Carbide Wire Roll for Enhanced Durability and Efficiency
Title: Global Manufacturer Launches Revolutionary Carbide Wire Roll for Enhanced Industrial PerformanceIntroduction:In a bid to revolutionize industrial productivity and efficiency, a leading global manufacturer has recently unveiled its groundbreaking YG15 Carbide Wire Roll. Incorporating cutting-edge technology and innovative design, this product promises to significantly improve the performance and longevity of wire rolling processes across various industries worldwide. [A brief company introduction can be included here, highlighting the manufacturer's expertise, global presence, and commitment to delivering high-quality industrial solutions.]Body:1. Overview of YG15 Carbide Wire Roll:The YG15 Carbide Wire Roll is a state-of-the-art wire rolling tool engineered to withstand the most demanding applications. Built with a base material predominantly consisting of tungsten carbide, this revolutionary wire roll exhibits exceptional hardness, wear resistance, and durability, making it a sought-after solution for industries dealing with wire production, coil manufacture, metal forming, and more.2. Key Features and Benefits:a. Unparalleled Durability: The YG15 Carbide Wire Roll boasts extraordinary resistance to wear and abrasion, ensuring a prolonged lifespan and minimization of downtime for maintenance and replacements. This translates into significant cost savings for businesses while maximizing overall productivity.b. Enhanced Precision and Consistency: The precision-engineered design of the carbide roll results in consistently accurate wire diameter control, enabling manufacturers to maintain tight tolerances throughout the production process. This feature is particularly crucial for industries where precision is paramount, such as automotive, aerospace, and electronics.c. Superior Surface Finish: The YG15 Carbide Wire Roll's unique surface finish leads to enhanced wire quality, reducing the need for additional surface treatments. By delivering a smooth and flawless surface, it enables businesses to meet stringent quality standards, while also reducing waste and optimizing operational efficiency.d. Versatility: This innovative wire roll is suitable for various wire rolling applications and can be easily adapted to different machinery setups. Its compatibility with a wide range of wire materials, including stainless steel, carbon steel, copper, and alloy, allows manufacturers to diversify their production capabilities and cater to different market needs.3. Impact on Industries:a. Wire Production: The YG15 Carbide Wire Roll's exceptional durability and precision make it an ideal tool for wire drawing and shaping processes. It enables manufacturers to improve wire quality, reduce surface defects, and enhance productivity, ultimately resulting in enhanced market competitiveness.b. Coil Manufacturing: In the coil manufacturing industry, the YG15 Carbide Wire Roll's ability to maintain consistent wire diameter control fosters the production of evenly wound coils with minimal variations. This leads to increased coil reliability, reduction in scrap, and improved operational efficiency.c. Metal Forming: Industries involved in metal forming processes, such as cold rolling, benefit from the carbide wire roll's outstanding wear resistance. It prolongs the service life of crucial rolling mill components, reduces maintenance costs, and ensures greater operational continuity.4. Future Prospects and Market Adoption:The introduction of the YG15 Carbide Wire Roll marks a significant milestone in the wire processing industry. Its versatile applications, superior performance, and remarkable durability are projected to drive the demand for this innovative product in various industrial sectors around the globe. With this pioneering solution, manufacturers can expect to achieve higher process efficiency, improved product quality, and a competitive edge in today's rapidly evolving markets.Conclusion:The launch of the YG15 Carbide Wire Roll by a leading global manufacturer underscores the company's commitment to delivering cutting-edge solutions that revolutionize industrial practices. With its exceptional durability, precision, and versatility, this innovative wire roll is set to redefine wire rolling processes across multiple industries, offering enhanced performance, increased efficiency, and improved product quality. As the market embraces this groundbreaking technology, manufacturers can confidently propel their operations into a successful and sustainable future.
Maximizing the Benefits of Tungsten Carbide in Cold Heading Applications
Tungsten Carbide Cold Heading: The Perfect Solution for Your Fastening Needs Fastening systems have come a long way in recent years with advancements in technology and material sciences. One such advancement in fastening systems is Tungsten Carbide Cold Heading. Compared to other materials, Tungsten Carbide Cold Heading has the ability to withstand extreme temperatures, wear and tear, and chemical reactions.With the increase in demand for fastening solutions, Tungsten Carbide Cold Heading has become the primary choice of many industries, including automotive, aerospace, and construction.What is Tungsten Carbide Cold Heading?Tungsten Carbide Cold Heading comprises a high percentage of tungsten carbide, typically ranging anywhere between 85%- 95%, mixed with a binding agent such as cobalt or nickel. The process of forming Tungsten Carbide Cold Heading involves compressing the material into shape while it's in its cold state.The compression process results in homogeneous grain structure, providing a unique combination of strength, hardness, and fracture toughness. The production process of Tungsten Carbide Cold Heading ensures that the material can withstand any amount of wear and tear and provide long-lasting, reliable fastening solutions.Applications and Advantages of Tungsten Carbide Cold HeadingTungsten Carbide Cold Heading is a versatile material used for various fastening applications. One of the primary applications of Tungsten Carbide Cold Heading is manufacturing cold-formed parts, including screws, bolts, nuts, and other fasteners.Due to the high energy absorption properties of Tungsten Carbide Cold Heading, they are also used in the construction industry to manufacture heavy machinery and equipment parts. Tungsten Carbide Cold Heading's resistance to wear and tear, resistance to extreme temperatures, and chemical inertness makes it suitable for use in harsh environments such as mining equipment and oil rigs.Another application of Tungsten Carbide Cold Heading is in the aerospace industry, where the material is ideal for manufacturing turbine engine blades and other aircraft parts. The unique characteristics of Tungsten Carbide Cold Heading, including its strength, wear resistance, and durability, make it the preferred material in the aerospace industry.Apart from this, several other advantages of Tungsten Carbide Cold Heading make it an ideal choice for various applications. For instance:1. Resistance to Wear and TearTungsten Carbide Cold Heading's high hardness, low friction, and exceptional wear resistance make it an ideal choice for applications that require lasting durability. The material can withstand high stress and maintain its shape, even under extreme conditions.2. High StrengthThe high strength of Tungsten Carbide Cold Heading makes it ideal for applications that require strong and durable fastening solutions. The material's strength makes it ideal for heavy construction machinery parts, aerospace turbine blades, and automotive engine components.3. Resistance to Extreme TemperaturesTungsten Carbide Cold Heading's ability to withstand extreme temperatures, ranging from -273°C to 500°C, makes it suitable for use in harsh environments. The material's resistance to high temperatures makes it ideal for use in the oil and gas industry, where temperatures can exceed 200°C.4. Chemical InertnessThe chemical inertness of Tungsten Carbide Cold Heading makes it an ideal choice for use in corrosive environments. The material's chemical stability makes it resistant to corrosion, erosion, and oxidation, ensuring long-lasting durability.5. High Fracture ToughnessThe high fracture toughness of Tungsten Carbide Cold Heading makes it suitable for applications that require resistance to cracking and damage. The material's fracture toughness enables it to withstand high impact forces, making it ideal for use in high-stress environments.Introducing the Leading Tungsten Carbide Cold Heading ManufacturerOur company is a leading manufacturer of Tungsten Carbide Cold Heading. We specialize in producing high-quality, reliable, and affordable Tungsten Carbide Cold Heading solutions for various industries. Our production process uses the latest technology and adheres to the highest quality standards to ensure that our products exceed your expectations.We take pride in our ability to provide excellent customer service, timely delivery of products, and expert technical support. Our team of experts works closely with you to ensure that our Tungsten Carbide Cold Heading solutions meet your specific requirements.Final ThoughtsAs the demand for robust, reliable, and durable fastening systems continues to grow, Tungsten Carbide Cold Heading has become the primary choice of many industries. The unique characteristics of Tungsten Carbide Cold Heading, including high strength, resistance to wear and tear, and robustness, make it an ideal material for use in extreme conditions.If you're looking for a reliable supplier of Tungsten Carbide Cold Heading solutions, look no further than our company. We specialize in providing high-quality Tungsten Carbide Cold Heading products that meet your specific requirements. Contact us today to learn more about our Tungsten Carbide Cold Heading solutions.
Unlocking the Secrets of Tungsten Carbide Hardness: What You Should Know
Tungsten Carbide: A Hardness That Knows No BoundariesTungsten carbide is a material that has been utilized in several industries for its ability to withstand extreme pressure and high-temperature environments. With the rise of technological advancements and the need for materials that can withstand these extreme conditions, tungsten carbide has become a crucial component of industrial manufacturing processes.Hardness, durability, and resistance to wear and tear are just a few of the advantages offered by tungsten carbide. As a result, it has become a go-to material in several industrial applications, including cutting tools, machinery, mining equipment and much more. What is Tungsten Carbide?Tungsten carbide is a composite material made from a mixture of tungsten and carbon atoms. It is produced by mixing finely powdered tungsten and carbon together, then heating the mixture at a high temperature in an inert atmosphere to produce a solid material.Tungsten carbide is an extremely hard and dense material that can retain its hardness even when exposed to abrasive and corrosive substances. It is highly wear-resistant, making it an excellent choice for industrial parts and components that require strength and durability in harsh environments.Why use Tungsten Carbide?Tungsten carbide is a material that offers several benefits to industrial manufacturing processes. One of the primary benefits of using tungsten carbide is its hardness. Tungsten carbide has a hardness that is second only to diamonds, making it ideal for applications that require extreme durability.Its high resistance to wear and tear, and its ability to withstand high-temperature environments also make tungsten carbide an excellent material for manufacturing tools and machinery, especially those used in the mining and drilling industry, where equipment needs to withstand tough and rugged terrains.Another benefit of tungsten carbide is its ability to withstand corrosion and abrasion. It does not easily rust or corrode, even when exposed to harsh chemical environments, making it an ideal material for applications where exposure to corrosion and other chemical reactions is inevitable.Applications of Tungsten CarbideTungsten carbide is used in several industrial applications in various industries, including cutting tools, mining tools, aerospace, oil and gas, and many others. Below are some of the most common applications of tungsten carbide:Cutting and Milling Tools:Tungsten carbide is used extensively in manufacturing cutting tools like end mills, drills, and burrs. The hardness of carbide makes it an excellent material for grinding, cutting, and drilling through hard materials like metals and stones.Mining Industry:Tungsten carbide is commonly used in the mining industry to manufacture parts of drilling tools. The rugged and harsh environments of mining operations require strong and durable materials, and tungsten carbide serves this purpose.Aerospace Industry:Tungsten carbide is used in the aerospace industry to manufacture parts and components for airplanes and spacecraft. Its durability, hardness, and high melting point make it an ideal material for aerospace manufacturing applications.Oil and Gas Industry:Tungsten carbide is used in the oil and gas industry to manufacture parts of drilling equipment. The high-temperature and high-pressure environments of oil and gas drilling require strong and durable materials, and tungsten carbide fits the bill.Conclusion:Tungsten carbide is a versatile material that has several applications across various industries. Its superior hardness, durability, and resistance to corrosion and wear make it an ideal material for manufacturing tools, equipment, and other components that require strength and ruggedness.As the need for more advanced and durable materials continues to rise, tungsten carbide will remain an essential component of industrial manufacturing processes. Although it is a compact but its hardness knows no boundaries.